Drive to Cut Fruit Grower Costs Drives Harvest Innovation
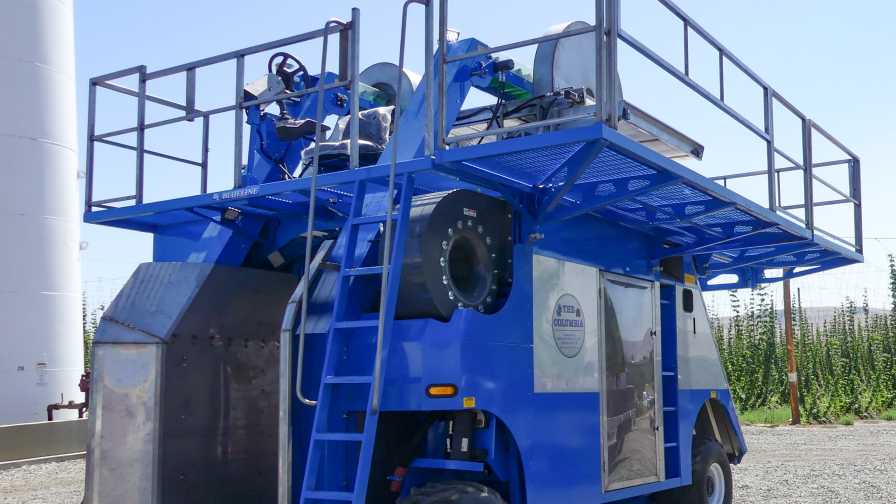
The BH300 is the latest berry harvester from Blueline, which utilizes a novel way of moving the crop using high-volume, low-pressure air, reducing loss to the ground by as much as 50%. Photo courtesy of Blueline
In talking with growers this season from his base in the Pacific Northwest (PNW), Gregg Marrs could feel tensions rising as the crops continued.
“Our growers are most concerned about enough labor to harvest their crops,” says the owner of Blueline Manufacturing and Equipment, Yakima, WA. “Mechanical harvesters for grapes and fruit are of the most interest at this time. Blueline is manufacturing harvesting machines for apples, grapes, and berries. We also import machines from five European countries to harvest these same crops.”
Blueline is on the front edge of using new technology in farm equipment, Marrs says, and it maintains that edge by constantly talking to growers not only in the PNW but also throughout the U.S. and around the world.
“We attend many international farm equipment shows in Europe to see how those countries are incorporating new technology, such as new sensors, cameras, and robotics,” he says. “Advancements in artificial intelligence and other technologies are advancing very fast.”
The new technology is most welcome, as Marrs says there is little doubt the agricultural labor shortage, which is being felt around the world, is going to become more acute.
“I see the lack of a stable, dependable labor pool as agriculture’s largest obstacle to profitability in the future,” he says. “We will continue to work to develop ways to increase worker productivity and grower profitability.”
QUALITY IS KEY
Reducing growers’ costs is essential, but at the same time, quality must not be compromised, says Kathryn Van Weerdhuizen. If anything, fruit quality must be improved, says the Market Manager, Berry, Vineyard & Olives for Oxbo International Corp., Lynden, WA. She outlined what the company is doing specifically in berries and grapes.
In the berry space, Oxbo has been working on multiple projects to increase product quality for mechanically harvested blueberries, primarily for the fresh market.
“Our Soft Surface kit for our blueberry harvesters reduces the impact to the blueberries, which can lead to damage and reduced shelf life,” she says. “We continue to work with growers and researchers to collect pack out, harvesting, interval, and varietal data.”
Oxbo also offers EvenFill, an onboard scale system that allows for consistent berry weights in the flat or lug, improving downstream efficiency.
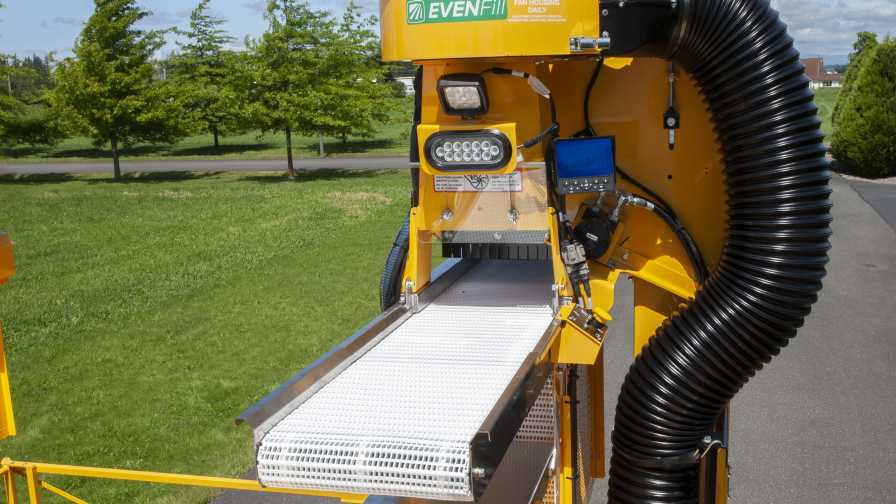
This Oxbo berry harvester features EvenFill, an onboard scale system. Here you can see the section of the tray with the load cell, the indicator light, and the display where you set the weight limit. Photo courtesy of Oxbo International
“Additionally, we have improved our selective shaking systems to get more of the ripe fruit off the bush on every pass — this improves fruit quality in subsequent mechanical passes,” she says. “For 2021, we’re introducing the Oxbo 7450, a top-loading berry harvester with increased capacity to improve efficiency in high-tonnage fields and in large plants.”
In the vineyard, Oxbo is working with customers mapping yield variability in the vineyard, and is introducing a new multi-function power unit, the 6030.
“The sprayer attachment for this power unit can also be configured with variable-rate spraying and spraying maps to increase efficiency and data on every block,” she says. “PremiumSort and PremiumDestem, which we have offered for several years on our vineyard harvesters, allow our equipment to deliver straight-to-tank quality fruit, which reduces the cost at the winery.”
GLOBAL SHORTAGE
European growers are also having problems finding enough labor to work in the orchards and vineyards, says Henri Michiels, Director (Innovation-Commercial), Munckhof Fruit Tech Innovators, Netherlands, creating a need for more automation. During the COVID-19 pandemic the situation has only become more acute, so the company is emphasizing the benefits of its Pluk-O-Trak Harvesting system.
“The Pluk-O-Trak is provided with new capacity measure-ment and e-driven conveyor belts with tracking and tracing of the apples/pears and bin containers/positioning,” he says. “Remote-controlled and protected harvesting and logistics will be the future for smart growers with less people/pickers.”
Michiels says the name of the game for today’s fruit grower is precision, and besides reducing labor, harvesters that are computer-controlled are going to be more accurate than those guided manually. Robotics are next on the horizon, with sustainability and reliability being the key drivers for the long-term health of the fruit industry for both growers and investors.