Matson Fruit Automates Storage With Robotics
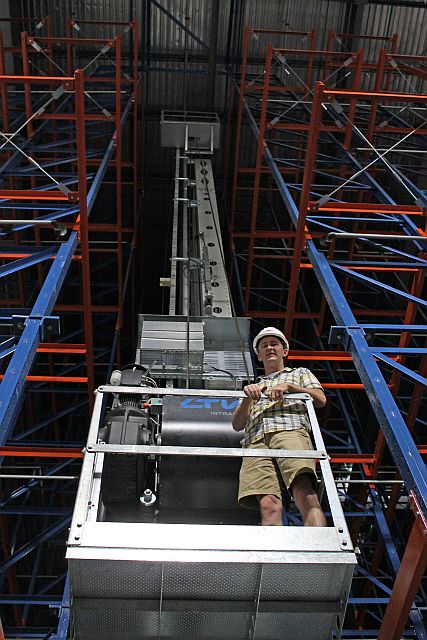
The new cold storage facility at Matson Fruit Company in Selah, WA, employs an automated storage retrieval system (ASRS). Robotic cranes retrieve the pallets, which allowed them to build a much taller facility, 73 feet, than a conventional cold storage warehouse. (Photo credit: David Eddy)
Of all the high-tech equipment that’s been installed by Pacific Northwest growers/packers/shippers over the past year, perhaps none is more state-of-the-art than the new cold storage facility at Matson Fruit Company in Selah, WA.
The system employs an automated storage retrieval system (ASRS) — in other words, it’s robotic. It is the brainchild of Jordan Matson, who’s in charge of the company’s shipping. What’s surprising is that Matson was not trained as an engineer, and is, a fact he mentions casually, a college dropout. (Though it should be noted that another native son of the Evergreen State who bears that burden is Bill Gates.)
Matson got the idea to use the ASRS system, which consists of a variety of computer-controlled systems for automatically placing and retrieving loads from defined storage locations, when he went to a material handling show in Cleveland, OH, in 2003. Matson Fruit had been using the same loading dock since 1982, and the company had grown 700% in that time, so it was clear that an upgrade was needed. Matson saw an ASRS system at the trade show, which was attended by people from all sorts of companies, from PepsiCo Inc. to UPS Inc. He was smitten.
“I love technology; I love electronics. Also, we were trying to reduce our reliance on labor,” he says. “I started brainstorming about how we could utilize it. Your imagination can run wild when you’re on an airplane for four hours.”
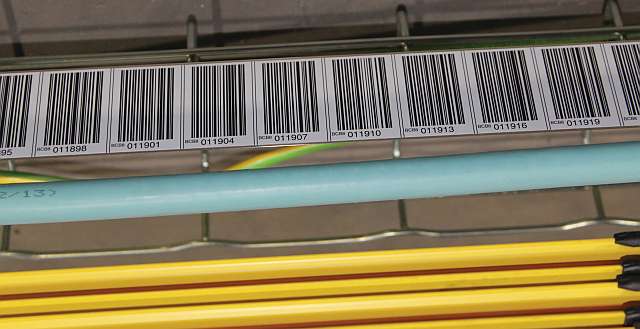
The robotic cranes at Matson’s new cold storage facility can “read” bar codes, enabling them to gather information about individual orders. (Photo credit: David Eddy)
Search Begins
Matson began touring the U.S., scouting ASRS systems. His company acquired property adjacent to their old facility, but they didn’t start construction on the ambitious project for more than a decade. For one thing, they had leased a cold storage facility that worked great. But last year they had to make a change.
“In 2013, the [facility’s] owners were selling it and we didn’t want to buy it, so we decided to build our own,” he says. “We got bids on all the equipment, settled on various vendors, and broke ground in early December.”
They chose Tri-Ply Construction for the building, which is designed for apples and pears in two different temperature zones, and Frazier Industrial for the racking. The key to the system, the automation, was handled by LTW Intralogistics, which is headquartered in Austria. Between April and October, Matson hosted several LTW teams, not just from Austria, but, also Germany, Idaho, and Oregon.
Matson Fruit started testing the system in early September, and is now using it 100%. Matson is more than satisfied with the company’s choice.
“I can log on with my cell phone or iPad and tell you exactly what capacity we are running at,” he says. “To me, that’s pretty nifty.”
It’s Automatic
Part of what makes the system so user-friendly is all Matson can program into the system. For example, he might have two orders for Galas from two different customers. Each of them says they want medium-sized fruit. But Matson knows Customer X prefers larger fruit and Customer Y prefers smaller fruit. So he enters that information about each customer, and that’s the fruit they will receive, automatically.
Another example: Kroger likes its pallets with corner boards and straps, Matson says. If it’s a Kroger pallet, it’s automatically sent to Value-Added. But some Kroger locations have smaller storage areas and want pallets with 42 boxes instead of the regular 49 boxes. Now that can be done automatically; people don’t have to remember.
“We take that tribal knowledge of our staff and code it into the system,” he says. “The more time you spend playing around with it, the more it makes sense. For example, when we’re sending pallets to Israel, we need legal information printed in Hebrew. They go to Value-Added, automatically.”
How Much?
Everyone wants to know how much such a system costs, and without putting too fine a point on it, Matson says it cost about 25% more than it would be to construct a more traditional facility of similar capacity. However, he hastens to add that right off the bat they are saving real estate, because they built up, not out. A regular facility with the same amount of storage would take three times the square footage.
Normally, pallets are configured three high and five deep. But at Matson’s new facility they are configured five high and two deep. Because the pallets are moved not by people driving forklifts, but by robotic cranes “reading” bar codes, the aisles are just 6 feet wide, much narrower than the traditional 16 feet.
There are other cost efficiencies as well. The company has 95-98% use of its pallet positions, compared to the industry standard of 70% of positions. The numbers get big in a hurry when you’re a big shipper like Matson. In a conventional facility, if you wanted to store 150,000 boxes of apples, you would need 4,000 pallet positions. But with this system, they would need just 3,150.
Because the pallets per square foot are so much denser with an ASRS system, there are other savings as well, such as on the considerable amount of power a cold storage facility requires. But the greatest savings is in labor, Matson says. He estimates that the company can reduce its staffing needs by 60%, perhaps more. It also changes the nature of the workforce from a huge staff to a small, dedicated team of information technology and maintenance specialists that really know their stuff.
“We don’t have to worry about the reliability of our workforce,” he says. “We don’t need a steady supply of forklift drivers, where those that are good [are always trying] to find a better job.”
A Trusting Father [Sidebar]
Jordan Matson, 32, is among the fifth generation of Matsons at 106-year-old Matson Fruit Company. His brother, Jason, runs the company’s orchards.
Representatives from LTW Intralogistics, the company that provided the automation for the new cold storage facility, remarked to Jordan that they had never had a client go from such archaic equipment to such a modern system in one leap.
“Most companies add technology incrementally,” Jordan says, “so there was a little trepidation on their part teaming up with Matson Fruit on this.”
Told that his dad, industry veteran Rod Matson, had shared a little trepidation of his own with Western Fruit Grower, Jason was unfazed. “I can’t blame him,” he says.