Estimates Vs. Actual: The Cost Of Installing A Vineyard
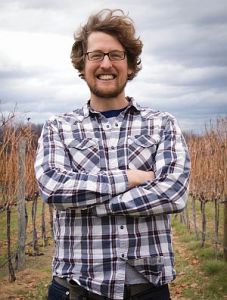
Tremain Hatch
The wine industry in Virginia is growing rapidly. We see many new wineries and vineyards now across the state. For these new operations and those on the way, I have been putting together resources that should help new growers estimate how much it costs to install a vineyard.
Picking up this project, I anticipated that it would be a simple matter of contacting various farm supply vendors and averaging together the different material costs for posts, wires and vines. That process can provide a fairly sound estimate; but it will not reflect all situations. I appreciate why growers need a reasonable estimate for budgets, business plans, and decision-making. But the actual cost of developing a vineyard? Well, it depends.
What are the big drivers of this variability?
Labor
Labor is the variable with the most play — and likely makes up the largest share of vineyard installation cost. Experience counts; one will be more efficient with labor installing their 100th vineyard than their first. We can all appreciate how experience can also make a big difference in terms of the quality of the work. Many factors have a bearing on how much labor it takes to install vineyard trellis, e.g. what posts are used, how they are driven into the ground, hand planting or mechanical planting, etc.
With many of our vineyards developed by individuals without a background in agriculture, sometimes contracting out the job is the most efficient way to proceed. If the job is contracted out, the variability between contractors’ pricing systems become apparent. Some contractors are more efficient than others, some want the job more than others — all these factors are important. The economies of scale are obvious in vineyard management — installation of a vineyard is no different. Bigger vineyards can usually be installed at a lower cost per acre than smaller vineyards.
Equipment
This column would be remiss if I didn’t mention considerations about the costs related to your equipment. The types and cost of equipment associated with developing and managing a vineyard can range dramatically. The choices you make can make or break the long- term profitability of the vineyard. Often there are cases where a small vineyard cannot return enough to justify the cost of a tractor and sprayer. The ratio between equipment cost and the number of acres that the cost can be spread across is a huge factor in deciding to develop a vineyard.
Materials
Material prices rise and fall in relationship to the commodity markets, but also reflect the differences in supply chains. Volume discounts are an important factor in the quantities of vines, posts and wire that are utilized in a new vineyard operation.
Costs also reflect the useful life of the material — posts that fail and must be replaced 10 years into the vineyard end up costing a quite a bit more than investing in a better quality post to start with.
Planting density also plays into the costs. Planting the vineyard at a higher density will drive up installation and material costs.
Location
The location of the vineyard will have a dramatic influence on the cost of its installation. There will be more vineyard installation expertise available in a county with a large wine industry compared to what you’ll find installing the first vineyard in your county. By nature, rural sites are far from supply and distribution networks — difficult-to-access sites can result in more expensive or slower deliveries.
Access roads may need to be constructed in order to move equipment out to the job site and the delivery of materials to the site. The site can make a difference too; we see many vineyards developed on rolling to steep topography. Installing a vineyard is more labor intensive and expensive on steeper land than flat land.
Putting It All Together
All farm operations are different; they reflect the differences in cropping systems, sites and owners. With that, the cost of production, even for the same production system can vary between farms. Situations vary. Excellent records will allow you to compare your real costs to those that you predicated; this verification will help make more accurate predictions in the future.
After inspection, installation of a vineyard closely resembles building a house. Not all three bedroom houses cost the same to build, and the same is true for vineyards. Benchmarks and estimations are useful information to help plan and make decisions, but remember that your on-the-farm results may vary.
Welcome Tremain!
Tremain Hatch is our newest Vine Lines contributor and has experience in vineyards in Italy, New Zealand, and Virginia. He works deliver innovative research to Virginia grape growers to improve their sustainability and fruit quality.
He has has completed a master’s degree in viticulture at Virginia Polytechnic Institute and State University. Tremain has been serving as a viticulture research and Extension associate with Virginia Tech since 2010.
American Fruit Grower recently sat down to talk with Tremain about his new post. Learn more about him here.