Innovation Turns Wafler Farms Into Orchard And Nursery Powerhouse
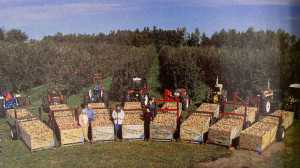
From left: Lois, Fritz, Kathy, Sue, and Paul Waller are the core of Waller Farms. (American Fruit Grower file photo by Samuel DeNoto)
Editor’s note, this story appeared in the November 1996 issue of American Fruit Grower and was written by Laura S. Burgard, assistant editor.
From humble beginnings as a migrant worker in 1952, Fritz Wafler has built up an orchard and nursery powerhouse that sells 200,000 nursery trees and 120,000 bushels of apples per year.
At 24, he came to the U,S. to gain experience to take back to his family farm in Switzerland, “I just wanted to come for a couple, three years,” he says. “I had no intention of staying.”
But after traveling through the U.S. and Canada for several years, working mostly in California, he met his wife, Lois, and took up residence in Wolcott, NY. In 1960, they started Wafler Farms on a run-down, 175-acre orchard, selling mostly vegetables for income while they grew their own apple trees from scratch.
More than 30 years later, at 1,100 acres, Wafler Farms, Inc. includes the apple orchard and wholesale nursery, as well as tart cherries, peas, and wheat, and until recently grew about 800 acres of beans. And the staff has expanded to include two of the Waflers’ three children and a daughter-in-law.
All In The Family
The children started working in the orchard and nursery as soon as they were capable, Fritz says. Two of them, Paul an d Kathy Wafler Madison, studied agriculture in college (Paul majoring in agricultural engineering at Morrisville College and Kathy majoring in general plant science at Cornell University) and came back to work on the farm after graduating. Son Walter is a research engineer at Xerox,
Paul manages the horticultural operations in the orchard and nursery and specializes in building custom equipment to make the field work more efficient (see sidebar “The Master Of Modification”), while Kathy manages the nursery sales and horticultural practices. Paul’s wife, Sue, also works in the office. Lois worked as bookkeeper for many years, and she still gives a hand in the office periodically.
Together, the members of the Wafler family have created a fine-tuned organization that is always striving to improve by staying on the cutting edge.
Experimentation Key To Advancement
In the orchard, the Waflers specialize in many apple varieties, including Empire, McIntosh, Ionamac, Crispin, Ionagold, and Gala. About one-third of the orchard is fully dwarf on M.9 rootstocks, spaced at 4 to 5 feet between trees and 15 feet between rows at about 600 to 700 trees per acre. Older semidwarf plantings are on interstem and M.26, A few of the processing varieties are planted on M.7 and MM.l11.
“The reason we didn’t plant M.9 earlier was because t ere was such a demand that we just kept selling it [from the nursery],” Kathy says.
Fritz says the Waflers will also be planting some Red Delicious soon on M,26, Most of the trees are trained on the slender spindle, central leader, and French axe systems. Trees are trained with a bamboo post that is tied to a top wire.
However, Fritz’s Swiss background — and his frequent travels to Europe to learn from other orchards — keeps the family constantly experimenting with new ideas in their own orchard,
“We try all kinds of things we see in Europe,” Fritz says,
The Waflers have tried several high-density systems. In one very high-density plot, Ionagold and Empire are planted on M.9 rootstock at 2 feet between trees and 11 feet between rows for ab out 2,000 trees per acre.
In the second growing season in the orchard, the Jonagold trees produced about 200 bushels per acre.
The Waflers had tried planting in double rows but found weed control difficult, so they are also experimenting with the Guttingen V and Mikado systems on Empire trees to increase density. Fritz learned both systems at the Guttingen Experiment Station in Switzerland, In the Guttingen V system, alternating trees lean in opposite directions,
“You have more trees per acre, but you have a single row, “ Fritz says.
Also, more light penetrates the canopy.
In the Mikado system, trees are trained to have three leaders for a very high-density orchard with fewer trees, and Fritz is trying a few trees with four leaders. Each leader is treated as a separate tree . However, while there are fewer trees (600 to 700 per acre}, the training cost is higher, Fritz says.
Both of the systems are very young, and Fritz says he has not seen enough to know if the yields will be worth the extra training costs.
The Waflers have tried other experiments on a small scale, such as ripping branches instead of cutting to prune. A regular practice in Germany and Holland, ripping damages the cells less, since the pruner is not cutting through them, Kathy says.
“If you look at it, it looks kind of crude,” says Fritz. However, there also seems to be less fire blight when branches are ripped, because the individual cells are not cut, he says.
The branch also heals faster and produces fewer suckers.
Not everything the Waflers have tried has worked. The double row planting made spraying and weed control difficult. When they tried bagging their small planting of Fuji apples last year, the timing wasn’t right, and they had problems with insects entering the bags, Fritz says.
Whatever they have tried over the years, the European influence is always present.
“The farms look neater than they do here.” Fritz says. “The whole thing looks neater.”
Cosmetics are important in Europe, he says, even including plan ting roses at the ends of rows for appearance. This neatness has rubbed off on Paul.
“I’m a real stickler for rep lacing trees,” he says. “I like it to be cosmetically pleasing.”
He has also devised machinery to make mowing and weed control as efficient as possible.
Conservative Management
Fritz credits hard work and good management for getting the family operation where it is today. A solid formula of conservative spending and keeping up with new developments and organizations has helped Wafler Farms grow bigger and more successful through the years.
Over time, Fritz has carefully monitored the growth of the operation and built it up steadily.
“I was spending conservatively,” he says. “If we had money, we bought it, and if we didn’t have it, we didn’t buy it. We bought some farm properties on contract or mortgages, but for most equipment we paid cash.”
In fact, when they first started the 700 per acre), the training cost is higher, Fritz says. Both of the systems are very young, and Fritz says he has not seen enough to know if the yields will be worth the extra training costs.
The Waflers have tried other experiments on a small scale, such as ripping branches in stead of cutting to prune. A regular practice in Germany and Holland, ripping damages the cells less , since the pruner is not cutting through them, Kathy says, “If you look at it, it looks kind of crude ,” says Fritz. However, there also seems to be less fire blight when branches are ripped, because the individual cells are not cut, he says, The branch also heals faster and produces fewer suckers.
Not everything the Waflers have tried has worked. The double row planting made spraying and weed control difficult. When they tried bagging their small planting of Fuji apples last year, the timing wasn’t right, and they had problems with insects entering the bags, Fritz says.
Whatever they have tried over the years, the European influence is always present.
“The farms look neater than they do here,” Fritz says. “The whole thing looks neater.”
Cosmetics are important in Europe, he says, even including planting roses at the ends of rows for appearance. This neatness has rubbed off on Paul.
“I’m a real stickler for replacing trees, “ he says. “I like it to be cosmetically pleasing.”
He has also devised machinery to make mowing and weed control as efficient as possible farm, they didn’t even buy apple trees for the orchard. Because they didn’t have the money to buy trees, and because Fritz couldn’t find semi-dwarf rootstocks commercially, he acquired some from Dr. Karl Brase at Cornell University’s Geneva Experiment Station. Brase was working with dwarfing rootstocks at the time, and the Waflers used his rootstocks to grow their own trees. They saved money and knew the quality of the trees they were planting.
The result: eventually, neighbors noticed the high-quality trees and asked the Waflers to grow some for them, prompting the beginning of the Waflers’ commercial nursery.
Fritz’s conservative philosophy still reigns today. And Paul’s customized equipment is designed to make field operations more and more efficient, which saves both money and labor.
Keeping In Touch
Staying current with the most up-to-date, sound horticultural practices and developments in the industry helps Waller Farms stay on the cutting edge. Fritz keeps constantly educated on new trends.
“I read papers from several countries to read up on the newest things. I tried to learn from other people’ s mistakes … made plenty of my own mistakes,” he says.
He also frequently calls and visits Cornell extension agents. He has traveled to or orchards and nurseries all over the world and organizes his own orchard group tours through Europe. (In) September (1996) he spent a week in the Czech Republic looking at some disease-free apples being developed.
The family is also involved in numerous horticultural associations. Fritz is currently a board member of the International Dwarf Fruit Tree Association and has also been a board member of the New York Apple Association and the U.S. Apple Association. Kathy is currently president of the New York Horticultural Association. Paul has been a board member of the New York Apple Association, and is President of Lake Country Storage, a co-op the Waflers helped form.
The first Lake Country Storage meeting was held at the Waflers’ kitchen table in 1979 with 10 growers from the area.
“There were mostly young farmers, with new plantings, and we were concerned about selling all the apples, “ Fritz says.
Today, almost all the original group is still together. It has been such a success that the members have expanded the facilities three times.
“The old building was designed to be increased ,” Kathy says . “They had the foresight to think it would grow. The old building was expanded twice and a new building was built on the same property. I expect they’ll expand again in the future.”
Six of the members of Lake Country Storage formed Empire Packing a few years ago an d were joined by one grower who is not a member of Lake Country .
“We wanted to pack our own apples, “ he says . “We thought we might find a better market.”
Successes like these are part of Wafler Farms’ strategy geared toward steady growth.
“Getting started, I saw opportunities. I wouldn’t say it was difficult, because I have always worked hard . That’ s the secret of success – hard work, “ says Fritz.
Apple A-Peel At Wafler Farms
Besides all their horticultural expertise and innovations, the Waller family has many talents .
Kathy Wafler Madison is in the Guinness Book of World Records for peeling the longest continuous apple peel.
In 1976, as part of a promotion at a local mall, she launched into the record books with a 2,068-inch apple peel, which ranged between 1/32 and ‘ /.0 of an inch wide.
Actually, this was an improvement over a previous record she had held.
She learned the technique from her father, Fritz, who was also a record holder several years earlier, but who never made it into Guinness because a cross-town rival beat out his peel before publication.
“It’s a special method,” Kathy says. “You don’t just peel it off. I score it first, then I go back and just lift the peel off. I know exactly how wide the peel will be.”
That record-breaking peel took 11 hours. It also got her spots on the “Live with Regis and Kathy Lee” and “Geraldo” shows a few years ago.
She traveled to Austria and was treated like a queen at a Guinness festival and has performed numerous demonstrations.
The Master Of Modification
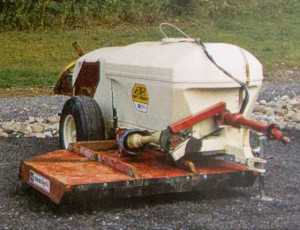
Hooking up a mower to his PTA sprayer gives Paul Wafler double duty in the orchard. (American Fruit Grower file photo by Samuel DeNoto)
One reason Wafler Farms is able to produce fruit efficiently and save money is that Paul Wafler has mastered the art of equipment modification. Rather than just be content to use a piece of equipment the way it was designed, Paul squeezes every possible use out of each piece.
To work in both the orchard and the field, Paul didn’t buy two tractors. He used a full-sized tractor, moved the gas tank from the side to underneath the body, changed the tires, and now enjoys a narrow orchard tractor with a full-sized cab.
Rather than investing in expensive electronic equipment to measure distances between trees with his orchard planter, Paul hooked a tire inner tube and a small micro -switch to a wheel frame, which triggers the tree to drop at the correct intervals. The inner tube is inflated so that the circumference equals the desired distance between trees.
Paul ‘s self-propelled tractor for hydraulic pruning lets the driver prune trees instead of driving the tractor. Four workers prune, powered by a 50-loot hose, while walking behind the tractor, and the tractor sets the pace. If the tractor gets ahead, a control which is fed from the leading pruner ‘s pocket through the tractor window to the gear shift pulls the tractor out of gear. If the workers catch up to the tractor, the lead pruner can push a lever through the back window to put it back into gear. A small electric motor controlled from the pruning shears steers the tractor. A tall flag mounted over the front wheel lets the workers monitor how close the tractor is to the trees.
To save trips through the orchard, Paul has hooked up mowers to his PTO sprayers. His side-mounted mower is driven by V-belts from the main PTO shaft and raises and lowers under the sprayer. Because it is offset and mows only one side at a time, it takes two sprays to complete a mowing.
It does take more horsepower to run the extra equipment, Paul says. “We’ve found that we’re really not saving any fuel, but we’re saving time.”
He also builds his own equipment to save thousands of dollars. The Waflers had bought a self-driving bin trailer for about $14,000. Since they typically use 10 bin trailers at a time during harvest, the expense seemed astronomical. So for less than $900 in raw materials, Paul built his own bin trailers and has even made some for other farms.
He has since decided not to use self-driving bin trailers, because they do not drive as fast as a tractor, and they have to travel a few miles to reach some orchard blocks.
If he’s not building a piece of equipment from scratch or remodeling an old piece, Paul usually buys the stripped-down model from a dealer and modifies it. He has even cut into spray tanks and reshaped them to accommodate extra equipment pulled by tractors.
“I guess the thing I’m notorious with the dealers for is when I buy a piece of equipment, the first thing I do is tear it all apart,” he says.